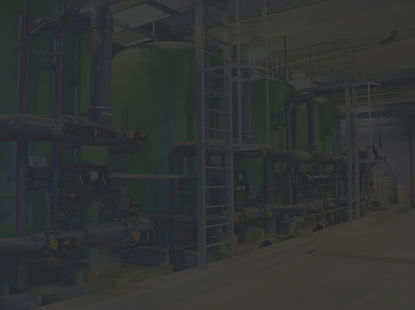
Immersion Cooling Filtration for Data Center Applications
​
As data centers evolve to manage increasing heat loads and power densities, immersion cooling has emerged as a cutting-edge solution for maintaining optimal operating temperatures. However, the success of immersion cooling systems heavily depends on maintaining the purity and quality of the cooling fluids. Industrial Filtration provides specialised filtration solutions designed to protect immersion cooling systems from contaminants, ensuring the long-term reliability and efficiency of your data center.
Immersion Cooling Advanced Protection
Single-Phase Immersion Cooling Filtration
​
In single-phase immersion cooling systems, where hydrocarbon fluids and esters are commonly used, maintaining fluid cleanliness is critical. Contaminants like particles, fibers, and moisture can severely impact system performance, leading to reduced dielectric strength, increased wear of moving components, and the formation of sludge.
Key filtration considerations for single-phase immersion cooling include:
​
-
Particle and Fiber Removal: Continuous mechanical filtration is recommended. This ensures the effective removal of particles and fibers from manufacturing residues, preventing contamination and preserving the dielectric properties of the cooling fluid.
-
Moisture Control: Effective filtration must also address moisture content, which can lead to sludge formation and water contamination in dielectric fluids. By removing moisture, filtration systems help maintain the integrity of the cooling fluid and prevent system failures.
-
Component Wear Prevention: Poor system hygiene or wear of moving components can introduce additional contaminants into the cooling fluid. High-performance filtration helps to capture these particles, ensuring that the cooling system remains clean and efficient.
Two-Phase Immersion Cooling Filtration
Two-phase immersion cooling systems, which involves fluorochemical fluids, require an even more robust approach to filtration. These systems must be capable of removing a wide range of contaminants, including water, oils, acids, and thermal decomposition products, to ensure reliable operation.
Key filtration considerations for two-phase immersion cooling include:
​
-
Removal of Hydrocarbons and Organic Contaminants: Hydrocarbons from wire insulation, silicone rubber, solder flux, and printed circuits can contaminate the cooling fluid. Carbon filtration is particularly effective in removing these hydrocarbons, ensuring the purity of the cooling medium.
-
Water and Moisture Removal: Condensation and hydrocarbon leaks can introduce water moisture into the system, which can compromise the efficiency of the cooling process. Advanced filtration systems are essential for removing water and maintaining the optimal condition of the cooling fluid.
-
Particulate Filtration: Particles from manufacturing residues can accumulate in the cooling fluid, leading to blockages and reduced heat transfer efficiency. The recommended filtration grade for two-phase immersion cooling systems is 1 micron and below, ensuring the removal of even the finest particles.
Why Choose Industrial Filtration for Immersion Cooling?
At Industrial Filtration, we understand the unique challenges of maintaining immersion cooling systems in data centers. Our filtration solutions are specifically designed to meet the rigorous demands of both single-phase and two-phase immersion cooling applications, ensuring the long-term reliability and efficiency of your systems.
​
-
Customizable Filtration Solutions: We offer a range of filtration products that can be tailored to the specific needs of your immersion cooling systems, providing the best protection against contaminants.
-
High-Efficiency Filtration: Our filters are engineered to remove a wide variety of contaminants, including particles, moisture, hydrocarbons, and more, ensuring the purity of your cooling fluids.
-
Expert Support: Our team of experts is ready to help you design and implement the ideal filtration solution for your data center’s immersion cooling systems.